New Assembly
Access to this feature may only be available with the ‘Complete’ edition. Ask your Wasp representative for details.
Assembly Items is an inventory item that is made of several items from your inventory, and it is considered one single unit. The items are removed from inventory to make the product. You can create Assembly Items using Inventoried, Non-Inventoried, Service items, and other assembly items. We recommend you read the Assembly Overview topic before you create Assembly Items.
This topic discusses:
Accessing the New Assembly Screen
Editing an Assembly
Note: The General Tab, Bill of Materials Tab, Prices Tab, Locations Tab, and Attachments Tab in the View/Edit Assembly Item screen is similar to the New Assembly Item screen.
Deleting an Assembly
Accessing the New Assembly Screen
Click on Item > New Assembly.
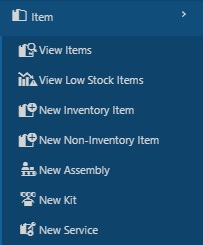
The New Assembly screen will appear.
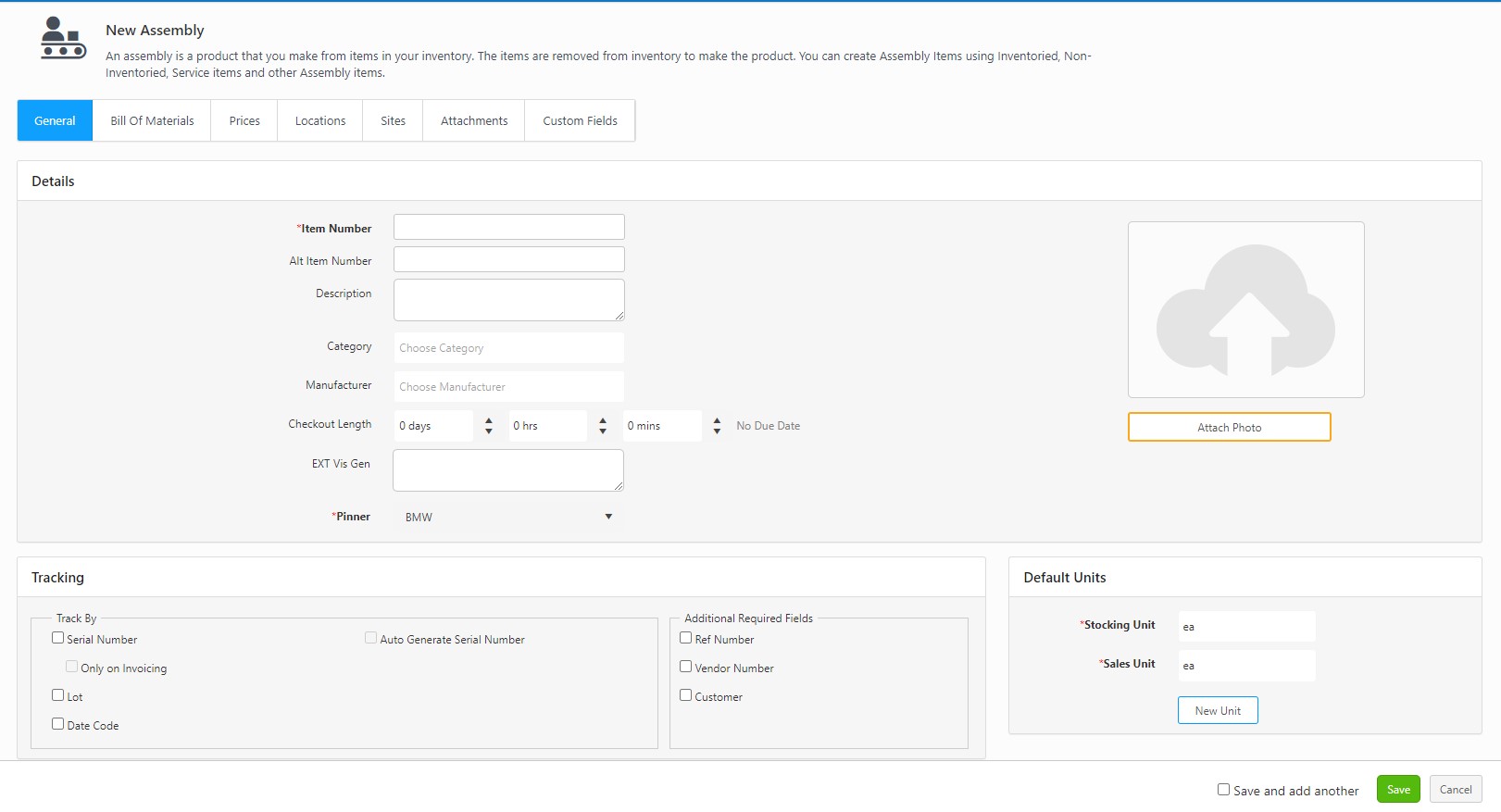
Adding a New Assembly
General Tab
The General Information tab is where you will enter the basic information to create a new assembly:
- Item Number (Required) - The Item number is often available on a barcode label already attached to the item, such as a UPC code or SKU number. Using an existing barcode for the item number allows you to scan or manually enter the number from each item as it comes in without printing and affixing your own barcode inventory item labels. Item numbers in InventoryCloud cannot exceed 31 characters.
Do not use a description as the item number. You should enter a numeric value in the Item Number field. A description of the item can be entered in the Description field.
Automatic Item Numbers: If the Automatic Item Numbers option is selected in Settings > Item > Automatic Item Numbers, the Item Number field will appear populated with the next number in the sequence. For example, if you just created item 1001, the next number will be 1002. For further information on this option, please refer to the Settings topic
- Alt Item Number (optional) - Enter an alternate item number.
- Description - Enter a description.
- Category - Select the category. This field is optional and provides another way to sort and group items. The categories you have already created will appear in a drop-down list.
- Manufacturer - Select the manufacturer. This is the entity that manufactured the item. This field is optional and provides another way to sort and group your items.
- Checkout Length - This field specifies the default period, in days/hours/minutes, that this Item can be checked out to a customer. Enter the value using the arrow up and down button.
- Tracking - This contains checkboxes that determine whether an item's Serial Number, Lot, and Date Code will be used to track its movement through your inventory. For a more detailed explanation of tracking fields, please refer to the topic Identifying Tracking Needs. When creating your item, it is important that you determine how you want to track each item. Typically, small items that are all the same may not need to have any Track Bys selected. Items such as printers may need to be tracked by Serial Number, so returns and maintenance can be properly tracked. Medical supplies or food may need to be tracked by Date Code and/or Lot. If you choose to trackby one or more of these fields, you will be prompted to complete them each time you perform a transaction, such as a check out, move, remove, add, etc., on this item. For example, if you are tracking item 2233 -VZ laptop by serial number. Now you want to move a quantity of 5 of this item from one location to another. You will be prompted to enter a unique and valid serial number for each laptop you are moving so your inventory can be accurately tracked.
Tracked By options cannot be changed after you add inventory to the item. If you need to change a tracked by item, you will have to remove all inventory from that item, delete the item and create a new record.
- Serial Number - Serial Numbers must be unique for each item and limit you to managing one item at a time. If the Only on Invoicing checkbox is selected, the serial number is only tracked on invoices (not check-ins, check-outs, etc.). Example - Equipment such as printers and radios or anything you need to know which specific item you are using.
- When you click on the Serial Number checkbox, a text box will appear below Auto Generate Serial Number. Click on the Auto Generate Serial Number checkbox to generate the serial number automatically. Click on the Format button to format the serial number in the Settings > Number Series screen.
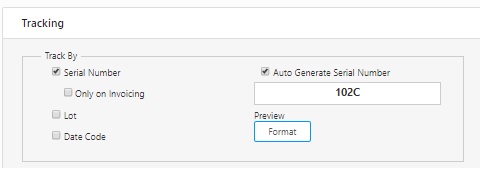
- Lot - These numbers are provided by the manufacturer to indicate from which batch these items were made. Example - Medical Supplies, Pharmaceuticals, Food products.
- Date Code - Date Code track the expiration or other "use by" date. Example - Food, Chemicals.
- Additional Required Field - This section contains checkboxes that acts much like the Tracked By boxes, but contains a different set of fields (PO, Vendor, and Customer) which are always available for use, even if they are not required. For example, if the option is not enabled for the Vendor Code field, a user adding inventory can enter a value for Vendor Code if he knows it or can skip entering the value if he doesn't. If this option is enabled, a value for Vendor Code is required to complete the transaction.
- Default Units (Required) - The default units section lists how you want your inventory to be stored. Refer How to use a Units of Measure of different types.
- Stocking Unit - Select the stocking unit. Examples: bag, barrel, basket, block, bottle, box, carton, container, drum, gallon, jar, pack, package, pallet, section, tub, vial, etc. When entering the stocking unit, you need to pick the smallest unit of measure that you will use to remove a whole item. A good test to use when deciding what the stocking unit should be is to think about your answer if you were asked to count how many of this item you have. If the answer is 100 feet of rope "feet or "ft" is the stocking unit. If the answer is 20 scanners, then "each or "ea." is the stocking unit. Each is common when the unit itself is not a standard unit of measure. If the answer is 100 boxes of nails then "box" or "bx" is the stocking unit. Refer How to use a Units of Measure of different types
- Sales Unit - This is the unit of measure used when you sell an item. For example - you may have a stocking unit of Carton which holds 10 boxes of nails, but sell them by the box. In this example, the Sales Unit would be the box. Refer How to use a Units of Measure of different types
- Pricing
- Cost (Required) - Cost specifies the amount your company paid to get this item into inventory. Cost handling in InventoryCloud is designed to show you the average cost and current value of your inventory. You can also use this cost information for other purposes, such as determining pre-tax and purchase order totals and receiving totals. This amount represents your cost for purchasing one of the base units for this item. If one Barcode Laser Scanner costs $300.00 you will enter 300 into the cost field. If you have items in your inventory that are sold in fractional quantities, you will need to decide which stocking unit to use. For example, if you have Rope as an item and it costs you $0.12 a foot, you would enter 12 in the Cost field and Feet as the Stocking Unit (entered on the Additional tab). If you rarely sell the rope in exact multiples of feet, you may want to enter your Stocking Unit as Inches, since this is the lowest unit measured, and enter your cost per inch in the Cost field. It is up to you how you want to calculate this; however, you should make sure that the Cost you enter is the cost for one whole Stocking Unit (either Feet or Inches, in our example). Keep in mind that you can enter a new cost on the Add Inventory screen if you purchase this item at a discount. For a detailed description for using Cost Tracking and Average Costing, please click here.
- Sales Price - This field specifies the price at which you sell an item. This field is for your information only and is not included in any reports. The price entered here is the price that appears in the Price field on Pick Orders. Note: If you want to lower prices on this and/or other items for a "sale period" at some point, you can quickly do this using the Mass Update feature.
- Cost Method - Select how you want InventoryCloud to calculate the cost for this item. Options are:
- Moving Average - When this method is used, the average cost of a particular item is recalculated based on each purchase. Cost is calculated on the item level.
- FIFO - When this method is used, the inventory that is added first is removed first. Cost is calculated on the item level.
- LIFO - When this method is used, the inventory that is added last (most recently) is removed first. Cost is calculated on the item level.
- List Price - This field specifies a manufacturer's list price for an item. This field is for your information only and is not included in any reports.
- Average Cost - This is a calculated value that averages the cost paid for the current quantity. This will be blank when entering a new item but will appear when you are viewing the Edit Item screen for an item that has inventory (quantity). When calculating Average Cost, the software does not include records that have an average cost of zero. When you run an Inventory Cost Report, the software does include zero-cost quantities when calculating Total Cost.
- Tax Code - You can optionally select whether this item is taxable or non-taxable.
- Dimensions - Enter the dimensions of the item after selecting the Height, Weight, and Volume Units.
- Attach Photo - You can add a photo if required.
- Click on the Attach Photo button. The Attach Files screen will appear.
- Click on the Select Files button.
- Drag and Drop - You can drag a file from a folder in Windows Explorer and drop it into the Attach Files window. Make sure the Select Files area is highlighted before dropping.
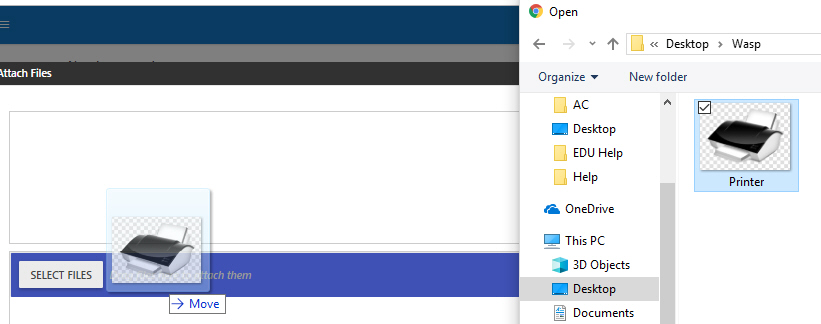
- Select Files - Click the Select Files button to open the standard Windows Explorer window. Navigate to the file you want to add, then click Open. The files you attach will appear in the window:
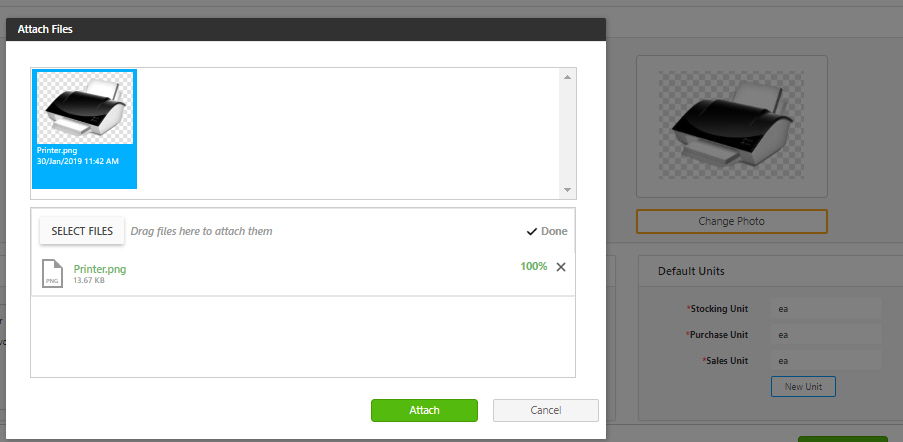
- Click on the Attach button. The photo will appear in the photo section. Click on the Change Photo to access the Attach Files screen and to select a different photo.
Bill of Materials
This tab lists all items that will be part of this Assembly when it is built.
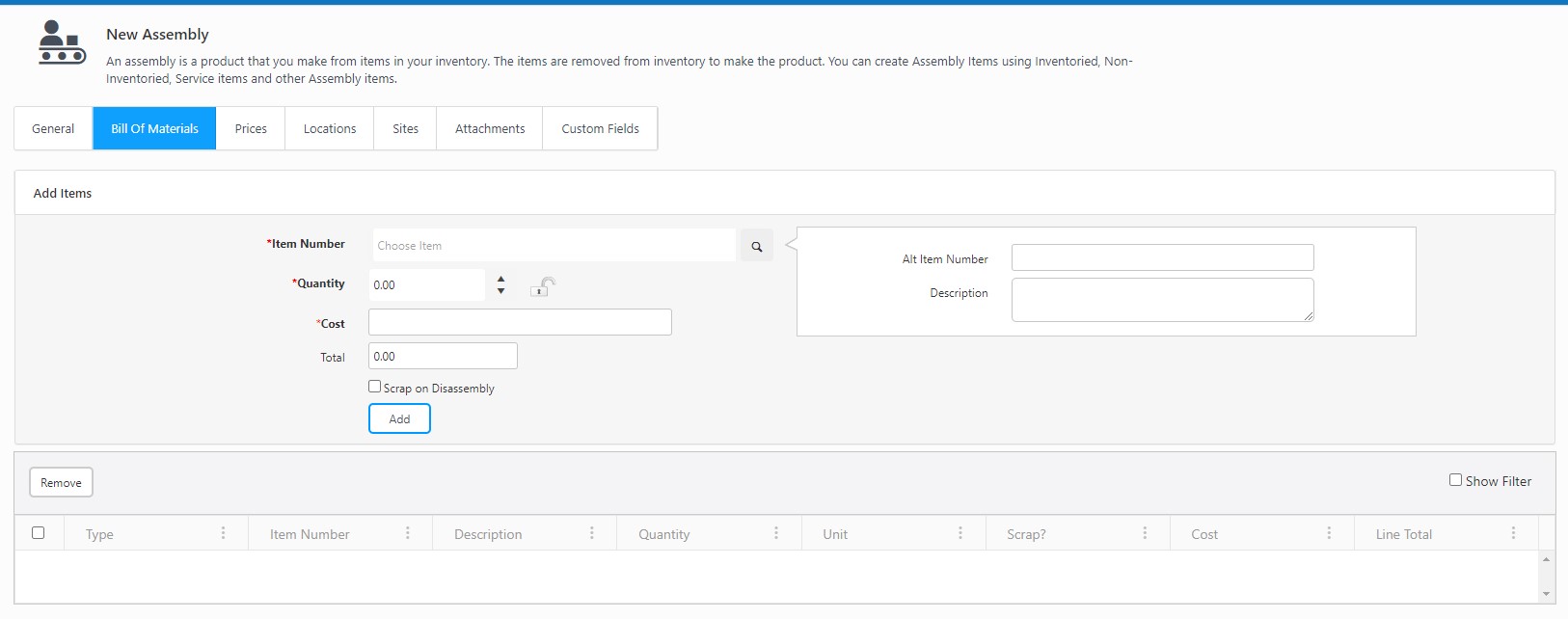
- Item Number (Required) - Enter the Item or select the item from the drop-down list. The Alt Item number and Description will automatically get populated on selecting the item number.
- Quantity (Required) - Enter the quantity of the item that is required to build this assembly item.
- Cost - This cost will automatically get populated if the value is entered while creating the item.
- Total - This field will update based on the Cost and the Quantity entered.
- Scrap on Disassembly - Select this checkbox if you want InventoryCloud to scrap this item if the Assembly item is disassembled. Refer to the Disassemble topic.
- Click the Add button when you have finished selecting the item. The item will be added to the list at the bottom of the screen. To remove an item, select the item by clicking on the checkbox and then click on the Remove button.

- Similarly, add more items to complete the bill of materials.
- Click on the Save button when you are finished adding items.
Prices
Tier pricing is a promotional tool that lets you price items differently for different products, categories, or customers. This is an effective way to move more merchandise.
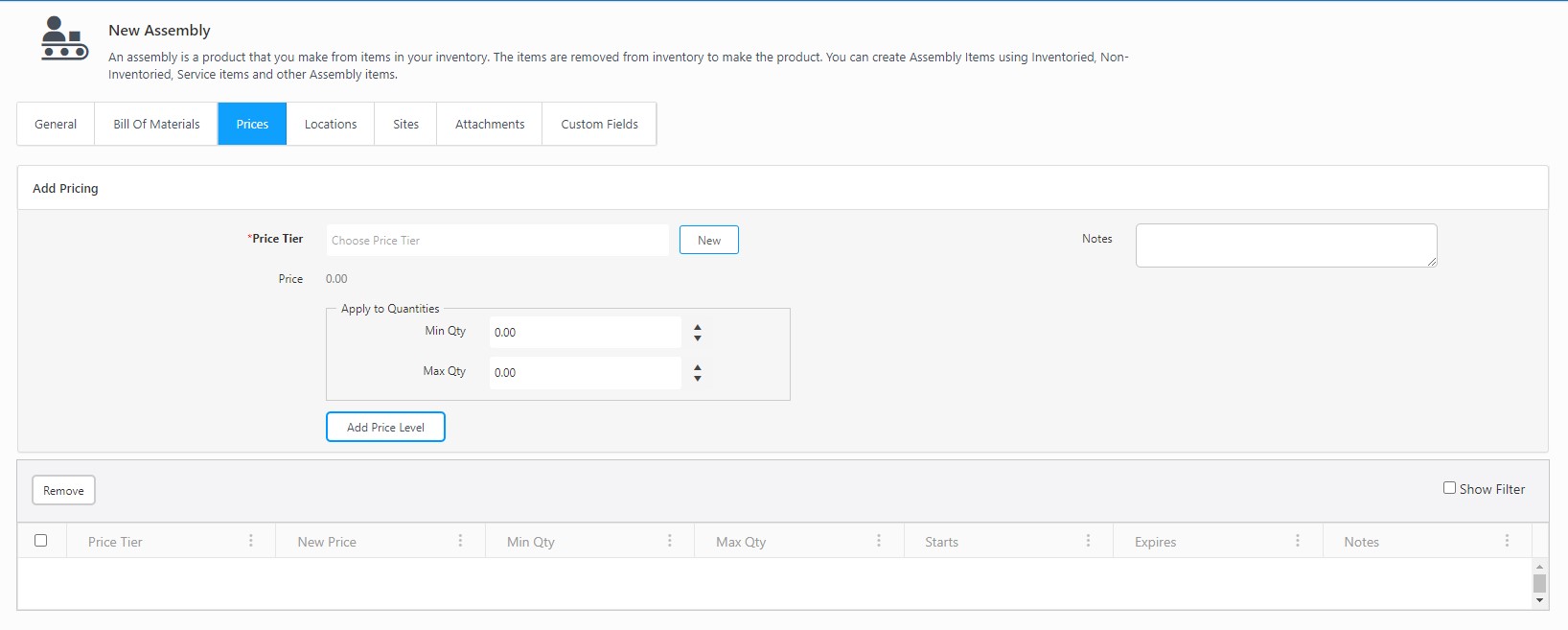
- Price Tier (Required) - Enter the price tier or select the price tier from the dropdown. Click the New button to access the New Price Tier screen.
- Min Qty - Enter the minimum quantity that must be purchased to qualify for this price tier.
- Max Qty - Enter the maximum quantity that can be purchased to qualify for this price tier.
- Notes - Enter any additional information in the notes field.
- Click the Add Price Level button to add the selected price level to the Assembly. The Price Tier will be added to the list at the bottom of the screen. To remove, select the price tier by clicking on the checkbox next to it and then click on the Remove button.

Locations
You can assign the assembly to specific locations.
To add a location:
- Location - Choose or enter the location name. You can also add a new location. Click on the New button, which will navigate to the New Location screen.
- Select the Primary Location checkbox if you want this to be the primary location for the item. In this scenario, when you Receive quantities of that item from a purchase order, they will automatically be assigned to the primary location. Also, when you Pick quantities of that item for pick orders, they will automatically be removed from the primary location. You can change these locations when picking and receiving if necessary. In addition, the primary location will appear in any location fields (on the Add inventory screen, for example), however; you can change the location if needed. The location tab will show the Site and Location name on hover.
- Min Qty - Enter the minimum number of assemblies that you want to have in stock for the selected location. This number can be 0 or positive; negative numbers are not allowed.
- Max Qty - Enter the maximum number of assemblies that you want to have in stock for the selected location. This number can be 0 or positive; negative numbers are not allowed.
- Reorder Qty - Enter the number at which you want to reorder this item for the selected Location. You can set an option in the software so that the system warns you at the login of any inventory items that have hit their reorder quantity. For further information on setting this option, please refer to the Inventory Settings topic.
- Add Notification - This is used to create an assembly low-stock notification for a location. If you want to receive a "Low Stock Item" alert, click on Add Notification button and configure the notification.
- Click on Add Location. You can remove a location by selecting the checkbox and clicking the Remove button.
You can use Show Filter to filter the location list and Group By to group the columns in based on your need.
Sites
You can assign an assembly to a specific site.
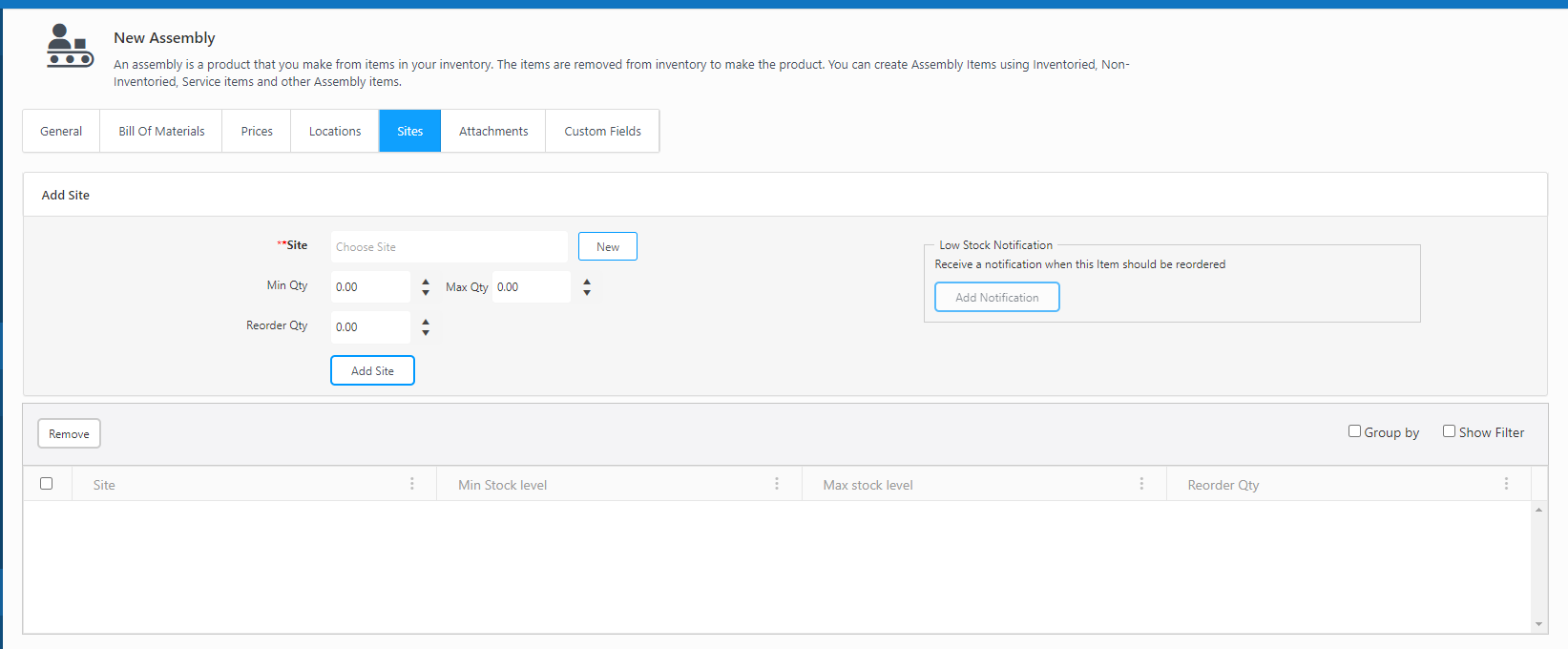
- Site - Choose or enter the site name. You can also add a new site. Click on the New button, which will navigate to the New Site screen.
- Min Qty - Enter the minimum number of assemblies you want to have "In stock" on the selected site. This number can be 0 or positive; negative numbers are not allowed.
- Max Qty - Enter the maximum number of assemblies you want to have "In stock" on the selected site. This number can be 0 or positive; negative numbers are not allowed.
- Reorder Qty - Enter the Reorder quantity. Reorder quantity is the amount that needs to be reordered whenever the item is below the minimum stock level.
- Add Notification - This is used to create an assembly low-stock notification for a site. If you want to receive a "Low Stock Item" alert, click on Add Notification button and configure the notification.
Note - The Low Stock Notification button will be disabled when creating/adding a new inventory item. On hovering above the notification button, a message will appear indicating, “Save your changes to your new item to enable creating notifications for it.” The user can create a Low Stock Notification alert while editing the item, i.e., the notification button will be enabled on the Edit Inventory Item screen.
- Click on Add Site. You can remove a site by selecting the checkbox and clicking the Remove button.
Use Show Filter to filter the site list and Group By to group the columns based on your needs.
Attachments Tab
To attach any document to this item, click on the Attachments tab:
Adding an Attachment:
- Click on the Attach Files button. The Attach Files screen will appear.
- Click on the Select Files button.
- Drag and Drop - You can drag a file from a folder in Windows Explorer and drop it into the Attach Files window. Make sure the Select Files area is highlighted before dropping.
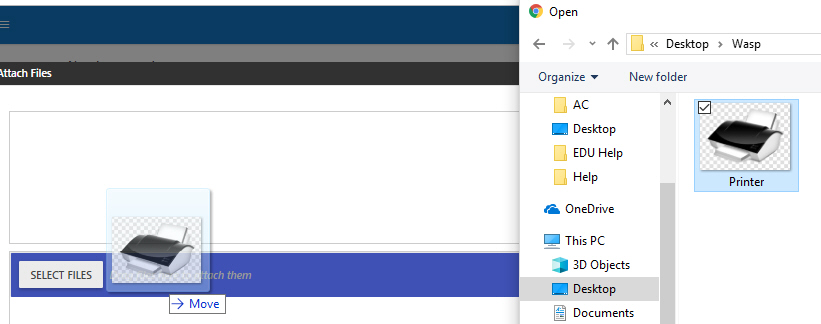
- Select Files - Click the Select Files button to open the standard Windows Explorer window. Navigate to the file you want to add, then click Open. The files you attach will appear in the window:
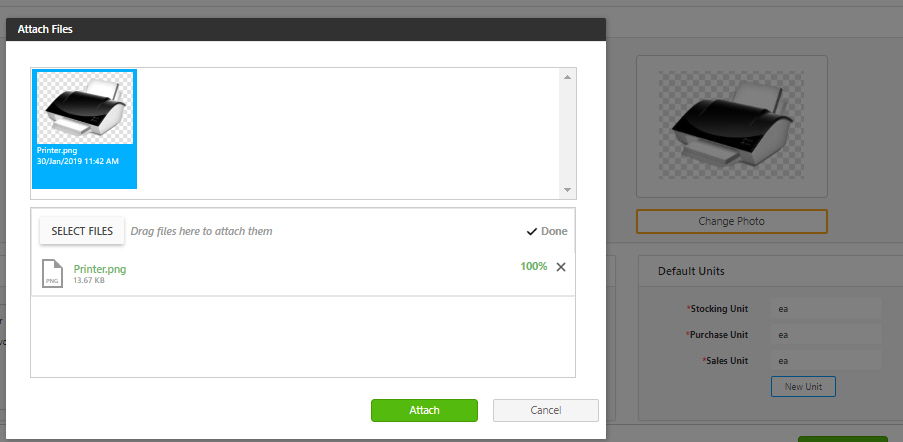
- Click on the Attach button.
Delete an attachment:
To delete an attachment, click on the trash can icon.

Edit an attachment name:
To edit the name of an attachment, click on the Edit button.

The File Name becomes editable.

Make changes as needed, and click on the Update button.
Saving the New Item
Once you complete entering all the information, click on the Save button at the bottom of the screen. The screen will navigate to the View Items screen, and a message will appear indicating that the item has been successfully created. It will also display the assembly name.
If you have more assemblies to create, you can select Save and add another checkbox before saving. On saving, the New assembly screen will appear again.
Editing an Assembly
- To edit an assembly, Click on Item > View Items.
- Search for an assembly that you want to edit.
- Click on the item number.

- View/Edit Assembly screen will appear.
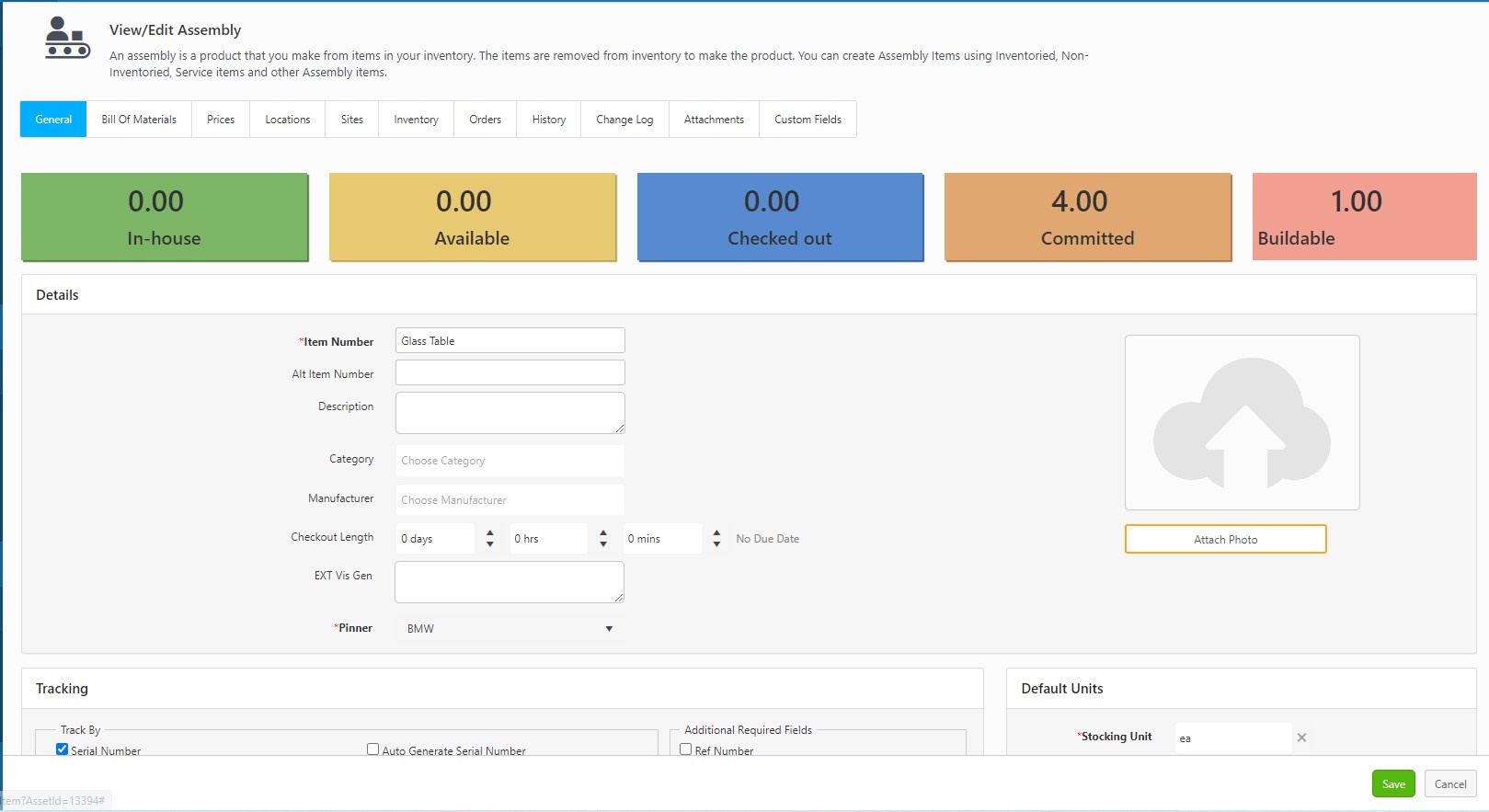
General Tab
The View/Edit Assembly screen will have three additional tabs - Inventory, Orders, Change Log, and History. Also, the screen will have the following colored boxes:
- In-house - indicates how many items you have.
- Available - indicates In-house qty - Checked out quantity.
- Checked out - indicates how many are currently loaned out.
- Committed - indicates how many are on pick orders but haven’t been picked yet.
- Buildable - indicates how many items are buildable.
Refer to Adding a New Assembly - General Tab, Prices Tab, Locations Tab, Sites Tab, and Attachments Tab for more details.
Inventory Tab
The Inventory tab will display the assembly's Site, Location, Total In House, Total Checked Out, and Total Available details.
- Show Filter checkbox allows you to narrow down the displayed results to a range of items or a specific item.
- Group By checkbox allows you to group the columns. Depending on how you want to view your information, you can have one group, two groups, or many groups.
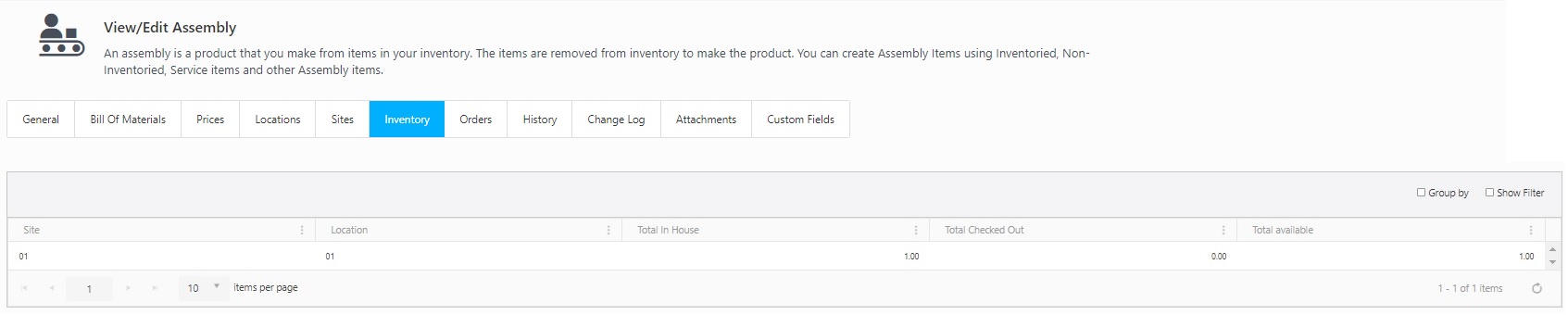
Orders Tab
The Orders tab will list the process orders (build order) and pick orders associated with the item. The orders tab will display the Order Type, Order Number, Order Date, Due Date, Order Status, Unit, Ordered Quantity, and Processed Quantity.
- Show Filter checkbox allows you to narrow down the displayed results to a range of items or a specific item.
- Group By checkbox allows you to group the columns. Depending on how you want to view your information, you can have one group, two groups, or many groups.
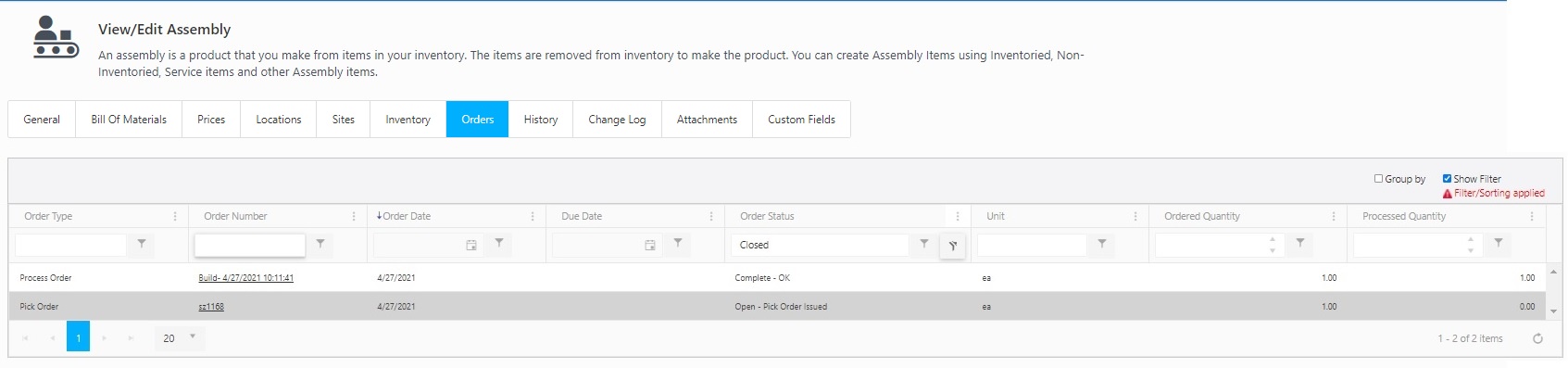
The Order Number is a link that will navigate to the View/Edit Pick Order screen / Build screen.
History Tab
The History tab will display all the transactions related to the assembly item. It will display the Transaction Date, Transaction Type, Site, Location, Quantity, Customer, User Transaction Date, Has Notes, and Has Signature.
- Show Filter checkbox allows you to narrow down the displayed results to a range of items or a specific item.
- Group By checkbox allows you to group the columns. Depending on how you want to view your information, you can have one group, two groups, or many groups.

Click on the Save button after updating the details in the View/Edit Assembly Item screen.
Deleting an Assembly
- To delete an assembly, Click on Item > View Items.
- Search for an assembly that you want to delete.
- Select the checkbox next to the item number and click on the Delete button. A confirmation screen will appear. Click on the Delete button again.

Note: You cannot delete an item that has a quantity or part of a Kit or a Bill of Material. A message "All Items could not be deleted" will appear on deleting.